The Myth’s and Realities of Robotic Welding Systems
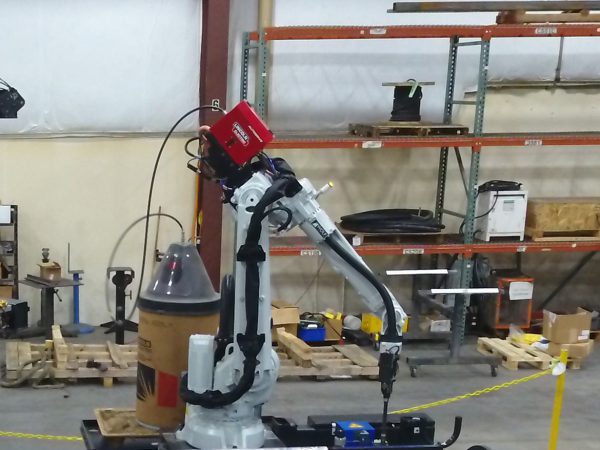
At Wolf Robotics, we often hear from many of our customers regarding their pain points such as:
- how they constantly have to adjust due to the lack of skilled welders
- the need to improve weld quality and consistency
- having to reduce costs to remain competitive
- the need to speed up production
These industry realities are why businesses, like yours, come knocking on our door for robotic welding solutions.
More often than not, first-time purchasers of robotic welding systems or other automation solutions (such as cutting, grinding, cladding) are nervous about the decision to try automation. They’re often concerned about making a costly mistake. We get it. Deciding to make a move into automation can be very intimidating. To help, in this article, we are going to address the myths and realities of automation focusing on robotic welding systems.
Automation Myths
1. It’s very, very difficult to program a robot.
2. Only high-quantity part production warrants a robotic welding solution
3. Using a robotic welding system will resolve all welding quality problems
4. The robot operator must be a highly trained and skilled programmer
5. Robotic welding systems are costly
6. A robot can weld any part
7. Robots shouldn’t be used to weld very large parts or assemblies (This is what we specialize in!)
Robotic Welding Realities
- Programming a robot is very easy and most anyone can learn how to program in just a couple days of training. There are three different ways to program a robot.
- Online Programming: Using the robot pendant, the programmer will jog the robot from point to point teaching the robot the weld path.
- Offline Programming: Using a program such as RobotStudio®, offline programming allows you to do the entire robot programming on a PC in the office without stopping production.
- Auto-Path Programming (CAR-W™): By downloading the CAD model into our auto-path programming software you can automatically program the weld paths without any programming needed. This is the best solution for high mix, low volume industries such as shipbuilding.
- You don’t have to commit a robotic welding system to the production of a single part. We have many customers who have programmed a robotic welding system to weld many different parts.
- If your parts have high variance, part fit-up is poor or if the part is not properly presented to the robot (tooling fixtures are very important), there will be problems with weld quality. Robotic welding is not right solution for every part. This why we work closely with our customers and advise them on the right solution for their specific parts and welding needs. In addition, we do offer software solutions that can help with part variance and part fit-up issues.
- Becoming an experienced welder takes years of experience. A robotic welding system operator only has to load the part, press the appropriate buttons to activate the machine, and then unload the part. Our cell controls actually make this job even easier. The training of a robotic welding system operator can often be done in just a few hours.
- We offer Fab-Pak pre-engineered systems that are often the perfect solution for first time automation buyers. These systems are affordable and offer the capabilities that support manufacturers of all sizes.
- A robotic welding system can’t weld any part that can be welded manually or semi-automatically. Clamping needs, access issues or specific positioning requirements may make the use of a robotic welding system unrealistic.
- Robot carriers and positioners allow the ability to weld very large parts. These robotic welding systems are usually custom solutions.
If you’re in the market for an automation solution, give us a call. We’re happy to help you make the right choice for your needs.